Quality
Quality Management Systems (QMS)
Independent Quality Assurance department is well in place having Robust QMS to ensure Product Quality at each stage of manufacturing
- Site Master File.
- Quality Manual.
- Validation & Qualifications system.
- Computerized System Validation
- Technological Process Validation.
- Calibration Master Plan.
- Vendor Management System.
- Document Control Management system.
- Review, approval and control of QC Test specification and procedures.
- Batch creation, Bach manufacturing data review and Product batch Release.
- Training Management system.
- Change control Management system
- Deviation Management system
- Investigations & CAPA Management
- Audit and Compliance.
- Audit and Compliance.
- Self -Inspection
- Audit and Compliance.
- In-Process Quality Assurance.
- Analytical Lab (QC lab) Assurance.
- Control Sample Management.
- Analytical Lab (QC lab) Assurance.
- Quality Risk Management system.
- Statistical evaluation of Quality attributes and system performance.
- Product Quality Review system
- Product complaints Management.
- Recall & Returned goods Management.
- Monitoring of Plant Preventive Maintenance
- Environment Controls within and outside manufacturing plants
Quality Control
Independent Quality Control Unit is well established for confirming the Product Quality
- Sampling, testing (chemical & Microbiological parameters) of Raw Material, Packaging Material, In-process and Finished Products as per standard specifications and compendia methods.
- Approval and release of Raw Material, Packaging Material, In-process and Finished Products.
- Stability studies of the product as per standard specifications and Guidelines.
- Environmental Monitoring for Microbial Attributes.
- Reference and Working standard management.
- Reference and Working standard management.
- Lab reagent Management
- Analytical data management done through Validated Laboratory Information System software system.
- Chromatographic instruments are connected with CFR Part 11 compliant Chromeleon and lab solution software to ensure Data Integrity Requirement.
- Analytical Data Trending and Laboratory investigation of OOT and OOS results.
Quality Policy
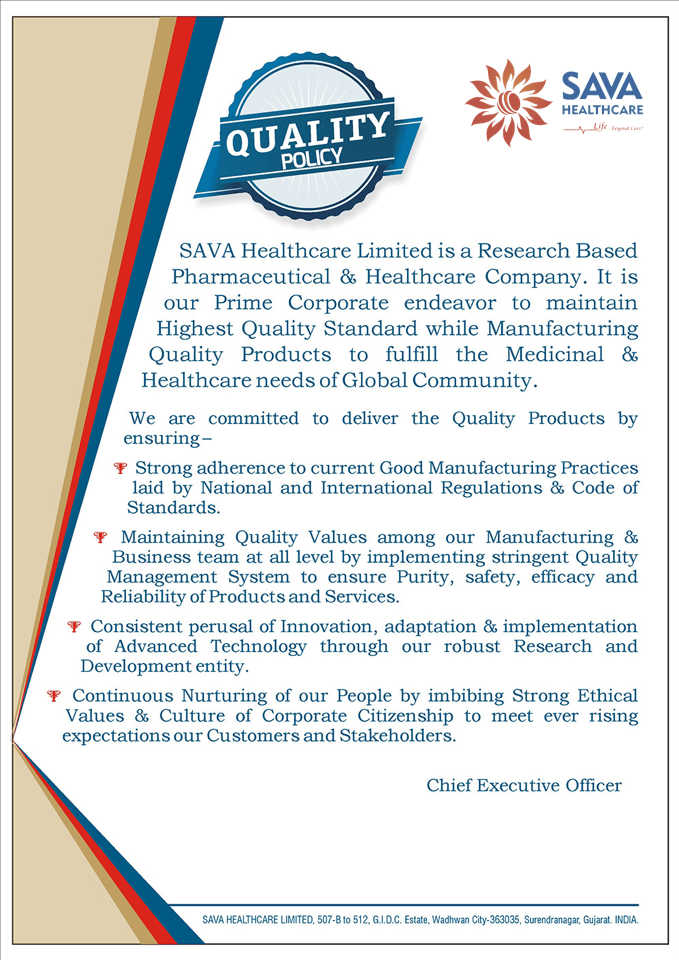
Environment, Health & Safety Policy
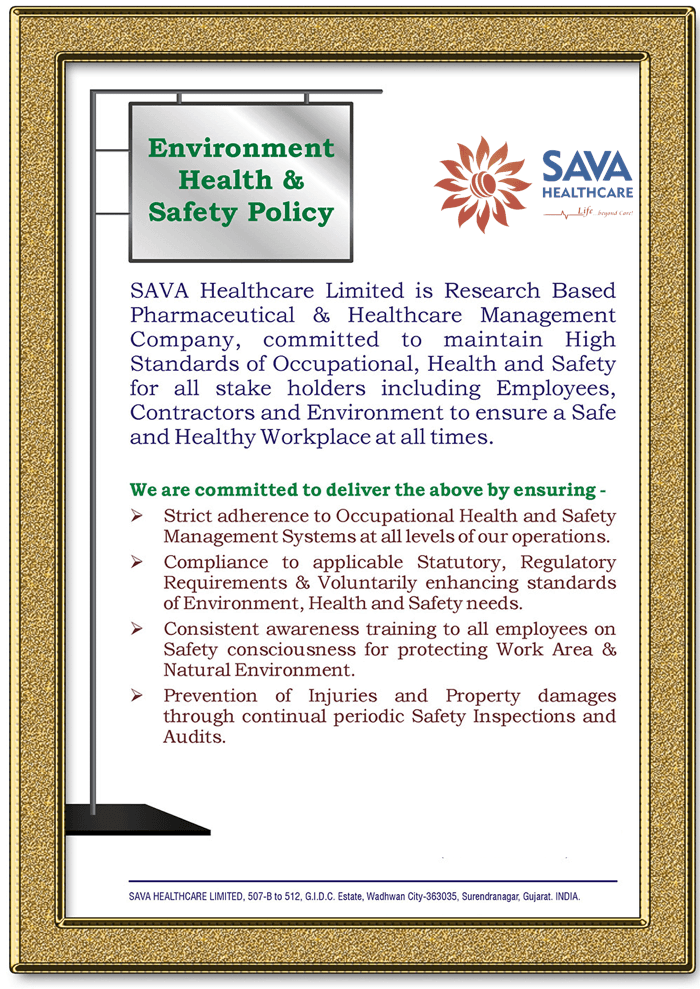